It is no secret that developing new materials for mechanical precision is a top priority in today’s manufacturing and engineering industries. Whether it be building robots to help with construction, crafting sophisticated medical tools or creating faster aircraft components, the need for stronger and more durable materials is growing rapidly.
The good news? We are making incredible strides in this area. The science of developing new materials is advancing immensely since its beginning and now, more than ever before, we have access to an array of options when it comes to material selection for our projects.
Looking To Develop New Materials For Mechanical Precision? Here Are Six Powerful Ways You Can Achieve It!
1. 3D Printing:
This new technology is revolutionising the way we approach developing new materials. 3D printing allows us to take physical models and turn them into fully-realised components in a matter of days or even hours. With this technology, we can quickly test new materials and determine what works best for our needs.
We are developing new materials in engineering that are stronger, lighter, and more cost-effective than ever before. The possibilities with 3D printing are truly astounding — and we aee just beginning to explore them. With each new breakthrough in the field of materials development, we are one step closer to creating products that will revolutionise the world.
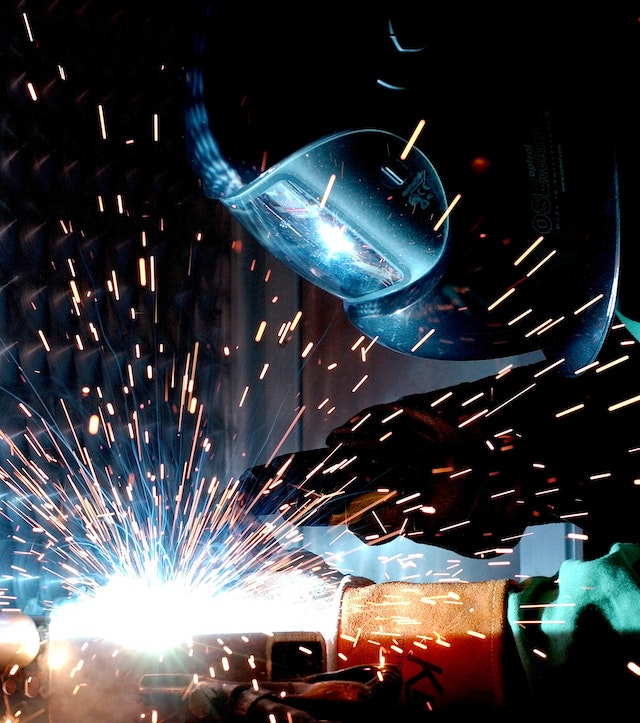
2. Additive Manufacturing:
Additive manufacturing (AM) simply refers to creating items by adding material layer by layer instead of cutting away material from larger blocks. This method is highly efficient and offers an extremely effective way of developing materials with greater accuracy than ever before.
The technology works for different purposes, including developing new materials that are stronger, lighter, and more durable than their mass-produced counterparts. With the potential to decrease production costs and waste, AM is a cost-effective alternative to traditional methods. It also has the potential to create parts with intricate geometries that are impossible to achieve using conventional processes.
AM technology is becoming increasingly important in different industries. Its ability to produce complex parts quickly and relatively easily makes it ideal for applications such as aerospace, automotive, medical, and consumer product manufacturing.
Furthermore, its ability to cut lead times and reduce material waste makes it a more sustainable option than traditional manufacturing techniques. All of these attributes combine to make additive manufacturing an invaluable tool for companies looking to increase efficiency or bring new products to market faster.
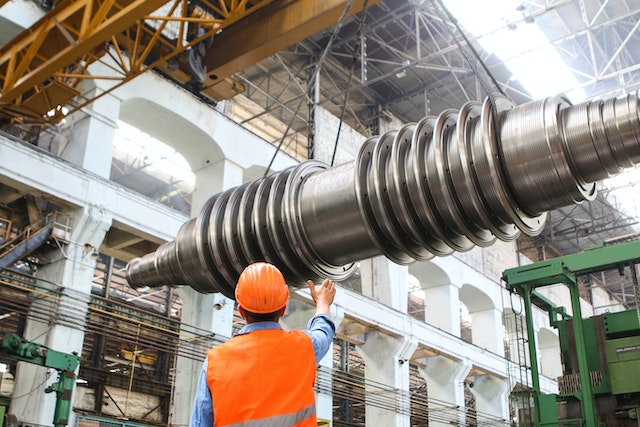
3. Composite Materials:
Composite materials are created by combining two or more different materials together to make something stronger, lighter, more durable or less expensive than any one material could be on its own.
Developing new materials with unique properties can meet the specific needs of each project. As a materials engineer, our job is to develop and test new composite materials for use in different applications. Our knowledge of the physical and chemical properties of different materials can develop new materials with specific characteristics.
We work with different projects over the years, ranging from creating lightweight aircraft parts to developing more durable and affordable building materials.
Our process at Aumic Engineering, begins by researching existing materials and their properties, then determining which combinations of materials will best meet the project goals. This involves testing combinations in a lab setting to determine how each material reacts when in combination with another.
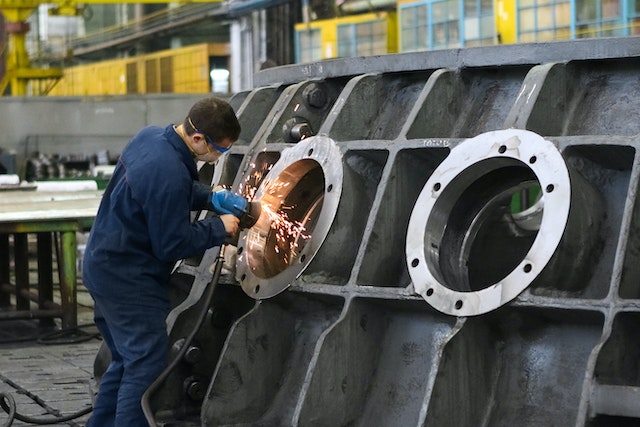
4. Nanotechnology:
The science of nanotechnology is allowing us to explore tiny particles and molecules on a microscopic level, providing us with an unprecedented ability to develop materials down to the very atom.
This means that we can create incredibly small, yet powerful substances for use in mechanical precision projects. By harnessing this newfound power, we can produce materials that are incredibly strong and significantly lighter in weight than traditional materials.
This technology can create materials for a variety of purposes, including medical sciences, manufacturing and security. The possibilities are endless when it comes to developing new materials with nanotechnology!
By embracing the potential of nanotechnology, you will gain access to an incredible range of advanced solutions that could revolutionise your industry. With the ability to craft groundbreaking products from the ground up – quite literally – you can leverage these resources in ways never before possible.
From creating stronger building structures and safer communications networks to using more efficient automotive components – the world is yours!
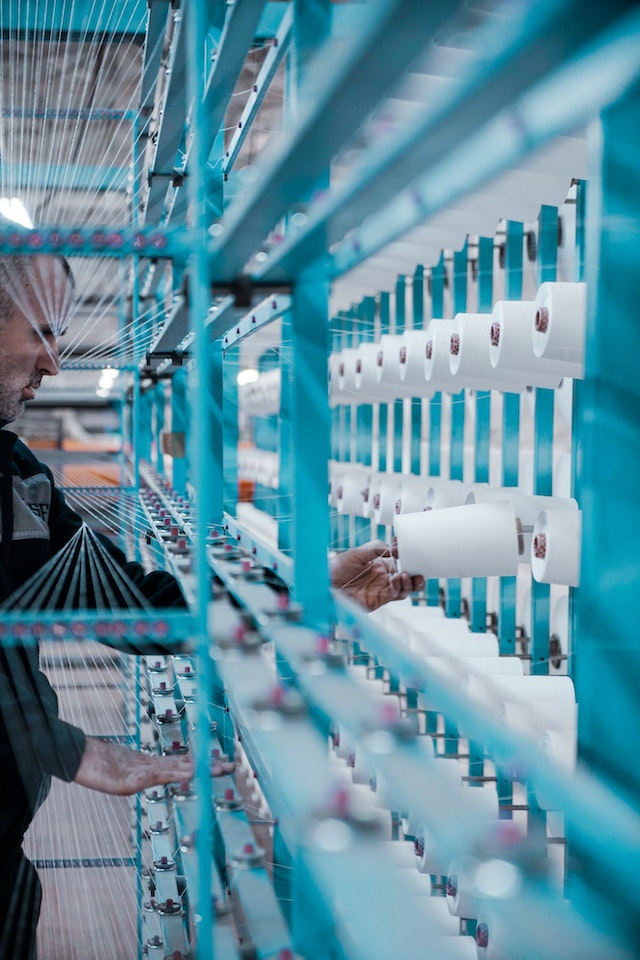
5. Shape Memory Alloys:
A shape-memory alloy (SMA) is made up of metal elements such as nickel and titanium, which allow them to remember their original shape even after being bent or stretched out of it. This makes them invaluable for applications where parts may need to undergo drastic changes in shape or temperature over time.
As an engineer, you may have interest in developing new materials using SMAs. The process of creating these materials can require extensive testing and analysis of the properties of different alloys that could work for your particular application.
It is also important to consider the potential risks associated with working with such a complex material. But if done correctly, the result can be a powerful tool that can drastically improve your product or design.
In addition to their shape-shifting properties, SMAs can create devices that respond to changes in temperature or pressure. Developing new materials like these are perfect for applications where precise control over how something will react to external conditions is required.
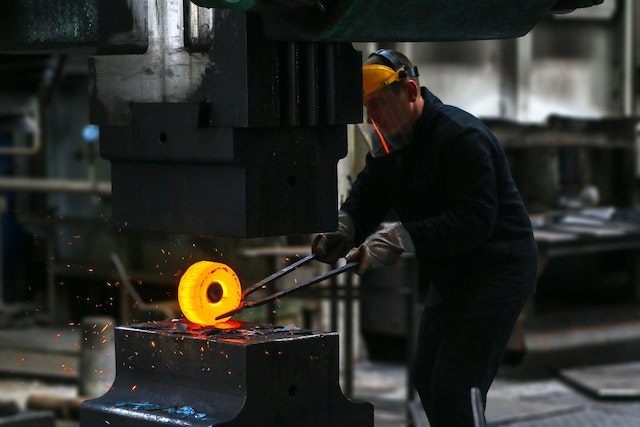
6. Smart Materials:
Smart materials are materials that can sense environmental stimuli and respond to them in a predetermined manner. These materials can create robust parts which react quickly and accurately to changing conditions, making them ideal for precision engineering applications.
By developing new materials with these properties, you can create parts that are lighter and more durable, while ensuring the highest level of accuracy. Smart materials offer an array of possibilities for engineers looking to take their designs to the next level.
With the right tools and know-how, you can revolutionise your design processes by using smart materials in innovative ways. Leverage this technology to give your projects unprecedented levels of precision, strength and durability. Unlock a whole new world of engineering possibilities with smart materials.
Developing New Materials For Mechanical Precision Are Limitless
We are continuing to explore new technologies and techniques while also finding ways to optimise existing processes such as 3D printing, additive manufacturing, composite material creation and more.
Plus, we are working hard on pushing our knowledge even further with things like nanotechnology, smart materials and shape memory alloys – all of which will help us to create even more powerful and effective materials in the future.
So, if you are looking for ways to start developing new materials for mechanical precision, know there are options available to you as we continue to build on our knowledge and make new advancements each day.
Contact us for more insight.
Read More
What Is CNC Precision Engineering And 6 Reasons Why It Is Totally Awesome.